This website uses cookies so that we can provide you with the best user experience possible. Cookie information is stored in your browser and performs functions such as recognising you when you return to our website and helping our team to understand which sections of the website you find most interesting and useful.
IoT System Development for Manufacturing Reinforced Composites
In reinforced composite manufacturing, there is a widely-used technique called vacuum molding. This technique is employed to create mechanical pressure on a laminate during its cure cycle. Vacuum molding helps to eliminate any voids (e.g. bubbles and wrinkles) in the buildup of layers and to achieve the optimal ratio of resin to reinforcement (e.g fiberglass, or carbon fiber) by squeezing out the excess.
In any vacuum bagging application, leaks are the biggest problem. Even the smallest leak can greatly hinder performance or even completely ruin a part.
To find leaks in vacuum bags, composites experts use special devices that allow for ensuring a perfectly sealed vacuum bag.
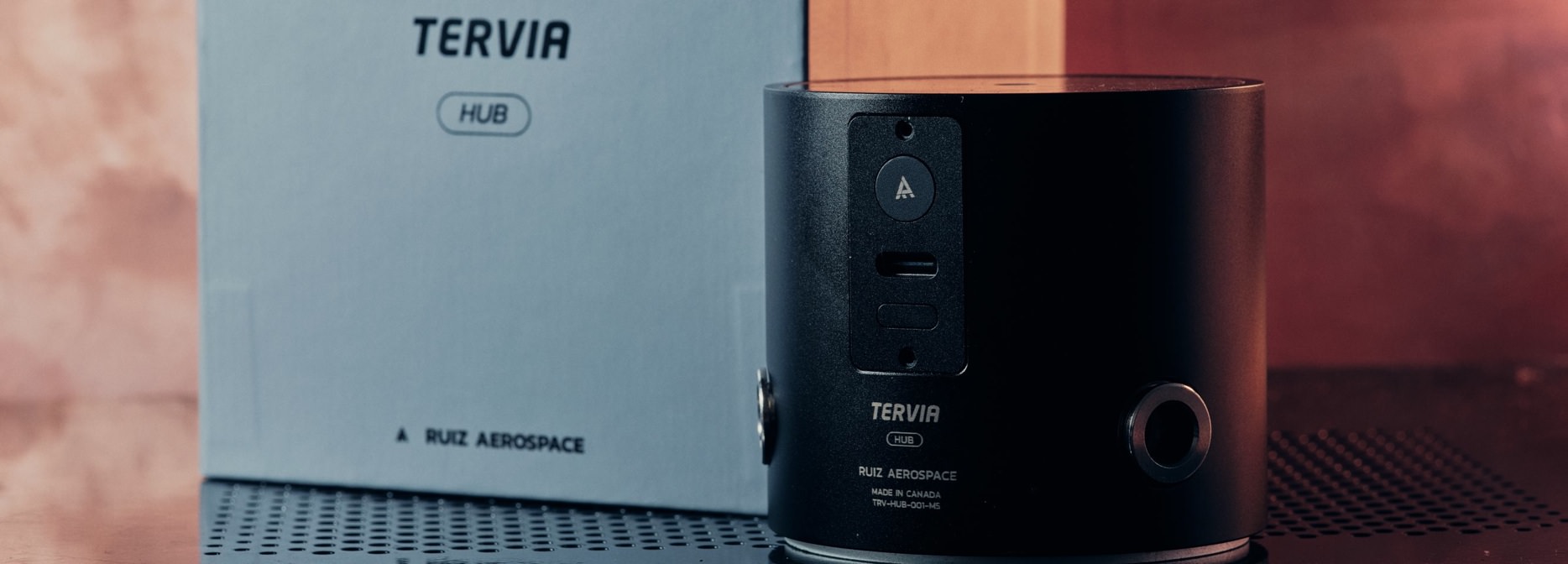
Request
A Canadian company developed an IoT solution that improves the way reinforced composites are manufactured. The solution is a special device that provides leak detection on a vacuum bag and communicates this information to the user via a phone, tablet or PC.
When this company turned to Integra Sources their solution was at the final stages of completion. But they faced a challenge: the data transfer from the cloud to the user application was slow. The delay in sending messages was about 250ms on the server side. In other words, the app failed to provide real-time performance.
Solution
After investigating the delays in data transfer between the Atlantic cloud platform and the end user apps, we offered a solution. Our team optimized the existing software architecture of the Qt cross-platform applications and implemented asynchronous techniques on the server which resulted in eliminating delays. Now the user apps receive data from the IoT devices in real time.
When the problem was fixed, our client decided to continue working with Integra Sources on the development of his solution. As part of our ongoing development activities, we implemented the migration of data from TinyDB to MongoDB databases, realized Google’s Protocol Buffers (an IoT communication protocol), and implemented Over-The-Air (OTA) firmware updates with our hardware development team.

Scope of work
- Optimized software to ensure real-time performance.
- Added new widgets to the user interface.
- Implemented OTA firmware updates.
- Migrated from custom communication protocol to Google’s Protocol Buffers (Protobuf).
- Configured the production server using the Atlantic Cloud platform.
- Implemented Windows plug-and-play driver support for the IoT device in firmware upgrade mode.
- Added a licensing verification mechanism that validates user licenses for using the software.
- Migrated from TinyDB to MongoDB database.
- Released applications on Windows Store, Apple's App Store, and Google Play Store.
- Implemented cloud monitoring tools for admin.
Technologies Used
- QT framework was used for the development of the cross-platform (Windows, Linux, iOS, Android) GUI applications for the end users.
- Tornado web framework was used for backend development for providing non-blocking network I/O and supporting thousands of network connections.
- AngularJS framework was used for frontend development (web interface).
- C/C++ language was used for firmware development (IoT devices).
Result
The IoT solution we helped to develop is a hardware device based on the Particle IoT platform. The device is built using an STM32 microcontroller and equipped with the Particle Wi-Fi module. It communicates with sensors that collect data on atmospheric pressure, vacuum, temperature, and humidity under the vacuum bag, and transmits that data to the custom Cloud where it is processed and saved.
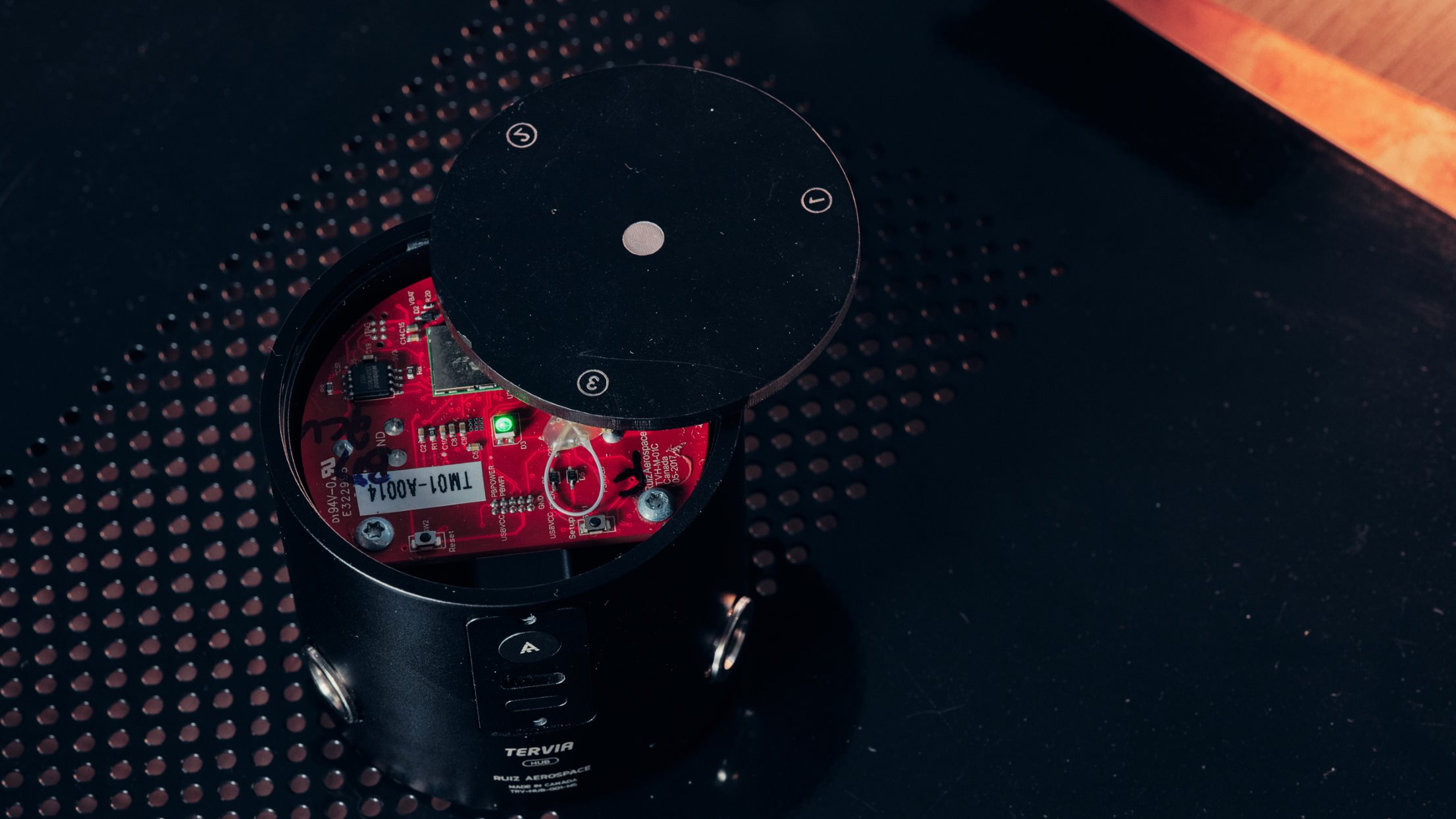
A composites expert places this IoT device on top of their vacuum bag setup and plugs in the vacuum lines to the device. To receive live data composites experts need to connect to the Cloud. They can do this with the help of apps for Windows, iOS, or Android available for PC, phones, and tablets. The app displays leaks on vacuum bagging tools so a user can quickly seal the bag and view the cure progress. It also records all manufacturing parameters such as pressure, humidity, and temperature.
The device has an innovative cure sensor to monitor the curing of individual parts. When the part is fully cured (cure parameters are met or threshold temperature is reached), users receive SMS or email alarms.
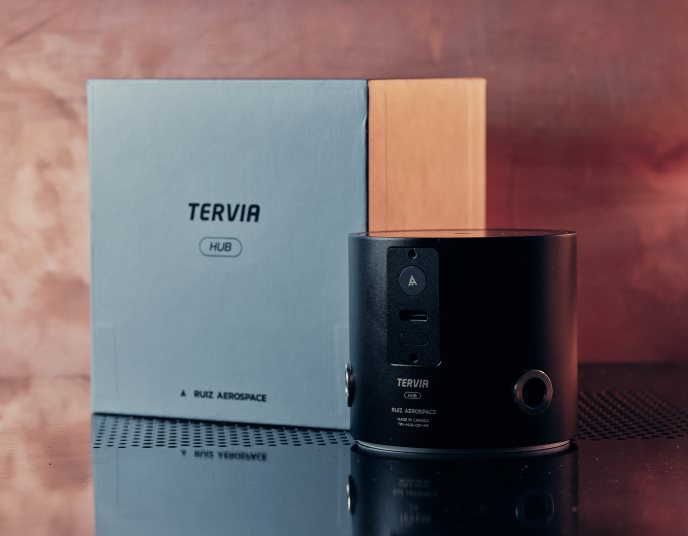
This IoT solution was recognized by the American Composites Manufacturing Association (ACMA). It won the 2018 Award for Composites Excellence (ACE) in Manufacturing, beating more than 600 other companies in the competition for this award.
Our team is currently providing full support for the IoT devices, the server, and the user applications, constantly adding new features.
The database has satisfied all scope requirements. The upgrades have improved communication and performance. Team strengths include accessibility and problem-solving and they are unafraid to research problems and develop their own solutions. Integra demonstrated strong management skills when they manage our servers for a week during an important trade show; we showcased our product at the event. Communication channels are always fluid and straightforward.
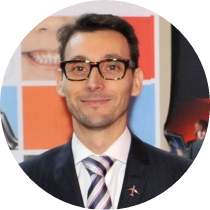
You might also like...

A Client-Server System for Test & Measurement Applications
We developed a licensing mechanism for the test and measurement platform and apps including a spectrum analyzer and an oscilloscope that can be accessed from a web browser
LEARN MORE
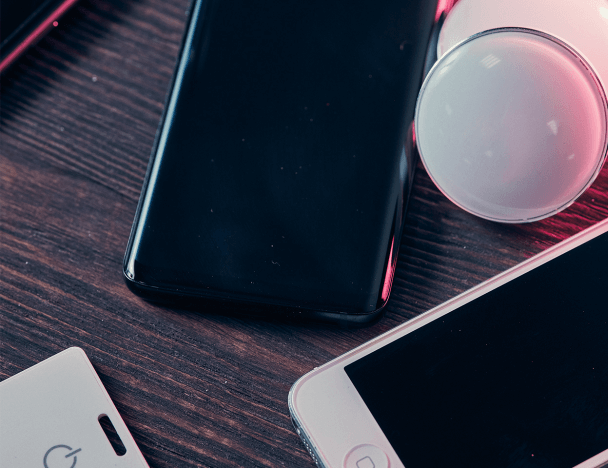
PaaS Solution for Building Location-Aware Services for Enterprise
The solution is an asset and people tracking system that consists of a network of Bluetooth beacons, a special gateway device, and an SDK for developers to build location-aware services
LEARN MORE